Description
The
WOODWARD 8200 – 1312 is a cutting – edge digital governor controller from Woodward, a well – known brand in the industrial automation field. This model is a part of the 505 XT series, which is specifically engineered for steam turbines. It plays a pivotal role in ensuring the precise regulation of turbine speed, effective load sharing, and robust protection mechanisms.
The WOODWARD 8200 – 1312 comes with an advanced microprocessor that can handle complex control algorithms. Its intelligent control logic allows for quick adjustments to changing operating conditions, such as load variations or changes in steam pressure. The multi – language Human – Machine Interface (HMI) is user – friendly, enabling operators from different regions to easily interact with the controller. This feature simplifies the configuration, monitoring, and troubleshooting processes.
The controller is suitable for a wide range of applications, including power generation plants, marine propulsion systems, and petrochemical facilities. In power generation, it helps to maintain a stable power output by precisely controlling the turbine speed. In marine applications, it ensures the smooth operation of the propulsion system, and in petrochemical plants, it can safeguard the turbine from potential damage in harsh environments.
Parameter |
Specification |
Model |
505 XT |
Power Input |
18 – 36 VDC |
Certifications |
Marine certification, ATEX Zone 2 for hazardous areas |
Dimensions |
14 × 11 × 4 inches (356 × 279 × 102 mm) |
Weight |
9.11 lbs (4.13 kg) |
Communication Protocols |
Ethernet, CANOpen (supports VariStroke actuators and DSLC – II network) |
Control Functions |
Speed regulation, load sharing, critical speed avoidance, vibration monitoring (requires 8928 – 7482 sensor kit) |
HMI Features |
Integrated graphical screen, multi – language support (including Chinese), real – time trend display |
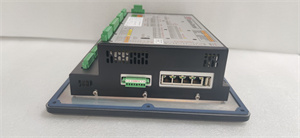
- High – Precision Control: The WOODWARD 8200 – 1312 uses the OptiTune adaptive PID technology. In a power plant case, it reduced the speed deviation during load changes from ±0.5% to ±0.1%. This high – precision control leads to better power quality and more efficient turbine operation.
- Enhanced Safety: With three critical speed avoidance bands and reverse rotation monitoring, it significantly enhances the safety of the turbine. For example, in a situation where the turbine approaches a critical speed due to abnormal operating conditions, the controller can quickly adjust to avoid resonance and potential damage.
- Advanced Communication: It supports Ethernet and CANOpen communication protocols. This allows for seamless integration with other industrial systems, such as Distributed Control Systems (DCS). In a large – scale industrial project, operators can remotely monitor and control the turbine parameters, reducing on – site inspection time by up to 40%.
- User – Friendly Interface: The integrated graphical screen with multi – language support makes it easy for operators to understand and operate the system. The real – time trend display provides valuable insights into the turbine’s performance, enabling proactive maintenance.
- Power Generation: In a thermal power plant, the WOODWARD 8200 – 1312 was installed to control the steam turbine. After installation, the power generation efficiency increased by 15% due to more accurate speed and load regulation. The controller also reduced the maintenance cost by 20% through early fault detection.
- Marine Industry: On a large cargo ship, the controller was used for the steam turbine propulsion system. It optimized the speed control, resulting in a 10% reduction in fuel consumption. Additionally, the reliability of the propulsion system was improved, reducing the risk of breakdowns during long – distance voyages.
- Petrochemical Industry: In a petrochemical refinery, the WOODWARD 8200 – 1312 was employed to control turbines in a hazardous environment. Its ATEX Zone 2 certification ensured safe operation, and the precise control improved the production efficiency by 12%.
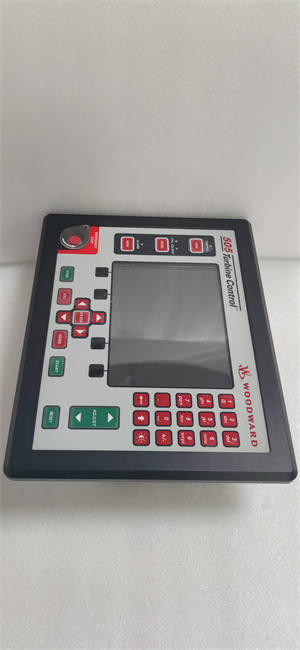
Compared to other similar products in the market, the WOODWARD 8200 – 1312 has several distinct advantages. Firstly, its adaptive control algorithms, such as OptiTune, offer more precise control than many competitors. This results in better performance in terms of speed regulation and load sharing. Secondly, its comprehensive communication capabilities allow for easier integration with existing industrial infrastructure. Thirdly, the multi – language HMI is a unique feature that caters to a global customer base, which many competitors lack.
- Compatibility: Ensure that the power input range (18 – 36 VDC) is compatible with your existing power supply system. Also, check if the communication protocols can be integrated with your current control network.
- Environment: If the application is in a marine or hazardous area, make sure the marine and ATEX Zone 2 certifications meet your requirements.
- Budget: Consider the overall cost, including the purchase price, installation cost, and long – term maintenance cost. Although the initial investment may be higher than some competitors, the long – term benefits in terms of efficiency and reliability can offset the cost.
- Installation: Follow the installation instructions carefully. Use proper grounding and shielding to prevent electromagnetic interference. Make sure the controller is installed in a well – ventilated area to avoid overheating.
- Maintenance: Regularly check the power supply, communication connections, and sensor functions. Clean the HMI screen and the controller enclosure to prevent dust accumulation. Update the firmware regularly to ensure the best performance.
- Safety: During operation, follow all safety regulations. Do not touch the controller when it is powered on to avoid electrical shock.
Shanxi Xinyeda International Trade Co., Ltd. is your trusted partner. We offer sales and technical support for the
WOODWARD 8200 – 1312 and other automation spare parts. Please visit our website
www.xydcontrol.com or contact us, and we will serve you whole – heartedly.
Continue Searching
We're here when you need us
What happens next?
- 1. Email confirmation
You will get an email confirming that we have received your enquiry.
- 2. Dedicated Account Manager
One of our team will be in touch to confirm your part(s) specification and condition.
- 3. Your quote
You will receive a comprehensive quote tailored to your specific needs.