Description
TRICONEX MP6004 is a high-performance modular processor module from TRICONEX, a leading brand in industrial automation and safety-critical systems. Designed to serve as the core controller in TRICONEX’s Tricon triple modular redundancy (TMR) systems, the
MP6004 delivers deterministic processing for safety-instrumented systems (SIS) and critical control applications. Engineered with advanced dual-core architecture and real-time operating systems, the
MP6004 ensures fast execution of control logic, precise synchronization, and reliable fault detection. This module is ideal for industries requiring ultra-high availability, such as oil and gas, chemical processing, and power generation, where system downtime can lead to severe consequences.
Parameter |
Details |
Module Type |
Modular Processor Module (TMR-based) |
Processing Core |
Dual-core ARM Cortex-A9 with real-time OS |
Memory |
2 GB RAM, 8 GB flash storage |
Data Processing Rate |
Up to 100,000 I/O operations per second |
Redundancy |
Triple modular redundancy (TMR) with auto-voting mechanism |
Communication Interfaces |
Ethernet (10/100/1000 Mbps), RS-232/485, USB 2.0 |
Compatibility |
TRICONEX Tricon V9/V10 systems, compatible with I/O modules and HMIs |
Operating Temperature |
-40°C to +65°C (-40°F to +149°F) |
Certifications |
SIL 3 (IEC 61508), ATEX, IECEx (hazardous area approval) |
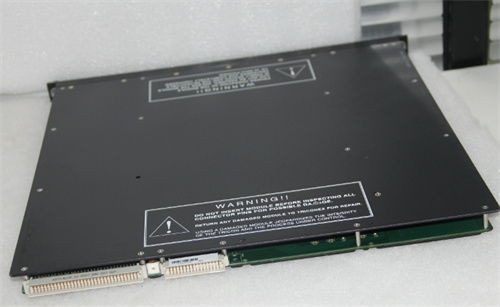
TRICONEX MP6004
The TRICONEX MP6004 excels in real-time control and fault tolerance, thanks to its TMR architecture that triplicates processing cores and enables self-diagnostic capabilities (built-in self-test, BIST). This design ensures that single-point faults are detected and isolated without disrupting system operation. For instance, in a large-scale refinery, the MP6004 managed over 5,000 I/O points with a response time of <50 ms, even during simultaneous processing of safety interlock logic and process control algorithms. Its dual-core design also supports parallel execution of control and safety tasks, enhancing overall system efficiency.
The MP6004 is widely used in industries requiring mission-critical control, including:
- Oil and Gas: Platform control systems, pipeline automation, and emergency shutdown (ESD) systems.
- Chemical Processing: Batch control, reactor safety systems, and continuous process optimization.
- Power Generation: Turbine control, boiler safety, and grid integration for renewable energy plants.
A notable application case involves a liquefied natural gas (LNG) facility that deployed the MP6004 as the central controller for its SIS. The module’s TMR redundancy ensured uninterrupted operation during a simulated single-core failure, maintaining control of cryogenic pumps and valves while automatically isolating the faulty channel. This resulted in zero downtime and full compliance with IEC 61508 SIL 3 standards.
Compared to non-TMR processor modules, the TRICONEX MP6004 offers inherent hardware redundancy without external failover mechanisms, reducing complexity and cost. Its dual-core architecture provides higher processing throughput than single-core alternatives, while support for diverse communication protocols (e.g., OPC UA, Modbus) enhances integration with legacy and modern systems. The module’s extended temperature range and hazardous area certifications also make it more robust for harsh industrial environments.
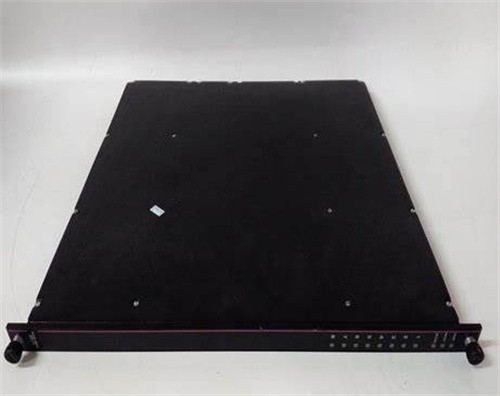
TRICONEX MP6004
When selecting the TRICONEX MP6004, consider:
- System Scale: Ensure the module’s I/O capacity and processing speed match the complexity of your control logic (e.g., small-scale vs. large distributed systems).
- Redundancy Needs: Verify if TMR architecture aligns with your safety integrity level (SIL) requirements and tolerance for single-point failures.
- Communication Requirements: Check compatibility with existing fieldbus systems (e.g., Profibus, Ethernet/IP) and integration needs with supervisory control and data acquisition (SCADA) systems.
- Future Scalability: Evaluate whether the module supports firmware upgrades and expansion options for future system enhancements.
- Installation: Follow TRICONEX’s guidelines for proper airflow and heat dissipation to maintain optimal operating temperatures.
- Firmware Management: Regularly update firmware to address security patches and performance improvements, using validated procedures to avoid downtime.
- Wiring Practices: Use shielded cables and isolated power supplies for communication interfaces to minimize electromagnetic interference (EMI).
- Testing: Conduct periodic functional safety tests (e.g., proof testing) to ensure compliance with SIL requirements and validate fault detection mechanisms.
Shanxi Xinyeda International Trading Co., Ltd. is your trusted partner, we provide and other automation spare parts sales and technical support. Please visit our website www.xydcontrol.com or contact us and we will be happy to serve you.
Continue Searching
We're here when you need us
What happens next?
- 1. Email confirmation
You will get an email confirming that we have received your enquiry.
- 2. Dedicated Account Manager
One of our team will be in touch to confirm your part(s) specification and condition.
- 3. Your quote
You will receive a comprehensive quote tailored to your specific needs.