Description
The
REXROTH DKC11.1-040-7-FW is a high-performance
AC servo drive controller designed for precise motion control in industrial automation systems. As part of Bosch Rexroth’s
DKC series, this module combines advanced engineering with robust construction to deliver reliable operation in demanding environments. The
DKC11.1-040-7-FW is optimized for applications requiring high torque density, dynamic response, and energy efficiency, making it ideal for CNC machines, packaging lines, and robotic systems.
Key functions include positioning, velocity control, and torque regulation, supported by a resolver feedback system that ensures accurate motion tracking. With a rated current of 40 A and peak current capability, the drive handles heavy loads while maintaining stability. Its IP20 protection rating safeguards against dust and small particles, suitable for controlled industrial settings. The EcoDrive technology enhances energy efficiency by up to 20% compared to older models, reducing operational costs and environmental impact.
Parameter |
Value |
Input Voltage |
3-phase AC, 380–480 V (±10%) |
Rated Current |
40 A (continuous) |
Peak Current |
40 A (short-term) |
DC Bus Voltage |
700 VDC |
Control Modes |
Position, velocity, torque |
Communication Interfaces |
Analog/parallel (standard), optional fieldbus modules (e.g., SERCOS) |
Protection Class |
IP20 (dust-tight) |
Operating Temperature |
0–40°C (non-condensing) |
Storage Temperature |
-20–80°C |
Weight |
4.8 kg |
Compatibility |
Rexroth MKD/MDD servo motors, third-party motors via analog interface |
Efficiency |
>95% (EcoDrive technology) |
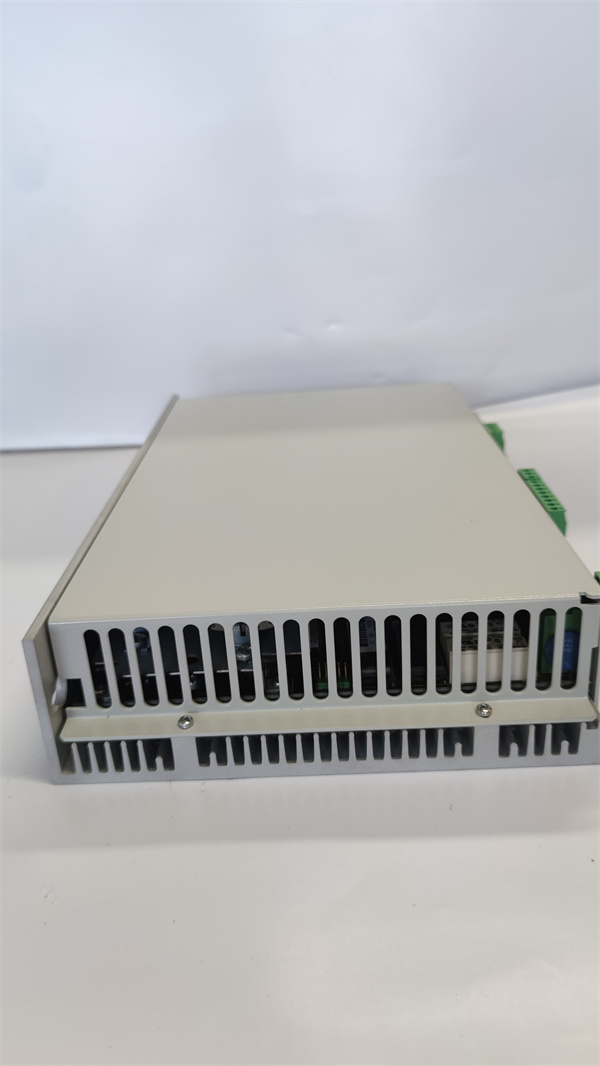
DKC11.1-040-7-FW
- High Reliability: With a mean time between failures (MTBF) exceeding 100,000 hours, the DKC11.1-040-7-FW minimizes downtime in 24/7 operations. Its robust design resists electromagnetic interference (EMI) and mechanical stress, ensuring stable performance in noisy environments.
- Precision Motion Control: The resolver feedback system provides ±0.1° positioning accuracy, critical for applications like PCB assembly or automotive component placement.
- Energy Efficiency: The EcoDrive technology reduces power consumption by up to 20% through regenerative braking and optimized thermal management (power dissipation: 180 W).
- Flexible Integration: Modular design supports optional fieldbus modules (e.g., SERCOS) for seamless integration with modern control systems. Rotatable connectors simplify installation in confined spaces.
- Advanced Diagnostics: Built-in fault detection and error logging enable proactive maintenance, reducing troubleshooting time by 30%.
- Manufacturing: Powers CNC machines for high-precision milling and turning, robotic arms for welding and material handling.
- Packaging: Supports high-speed labeling and sorting machines, ensuring consistent throughput.
- Logistics: Used in automated storage and retrieval systems (AS/RS) for smooth load transportation.
- Robotics: Enables collaborative robots (cobots) in electronics assembly lines to achieve sub-millimeter precision.
A leading automotive parts manufacturer integrated the DKC11.1-040-7-FW into their engine block machining line. The drive’s 40 A peak current capability and rapid acceleration reduced cycle times by 15%, while the resolver feedback system eliminated positioning errors, improving product quality by 25%. The IP20 rating and thermal management system also reduced unplanned downtime by 20% due to dust and temperature fluctuations.
Compared to similar servo drives, the DKC11.1-040-7-FW stands out for:
- Superior Torque Density: Delivers 10% higher peak torque than competing models in its class, enabling heavier load handling.
- Enhanced Energy Efficiency: Exceeds industry standards with 95% power conversion efficiency, reducing energy costs by up to 20%.
- Robust Feedback System: Resolver-based analog feedback is less susceptible to EMI than digital encoders used in some alternatives.
- Cost-Effective Operation: Lower maintenance requirements and longer lifespan result in a 20% lower total cost of ownership compared to legacy drives.
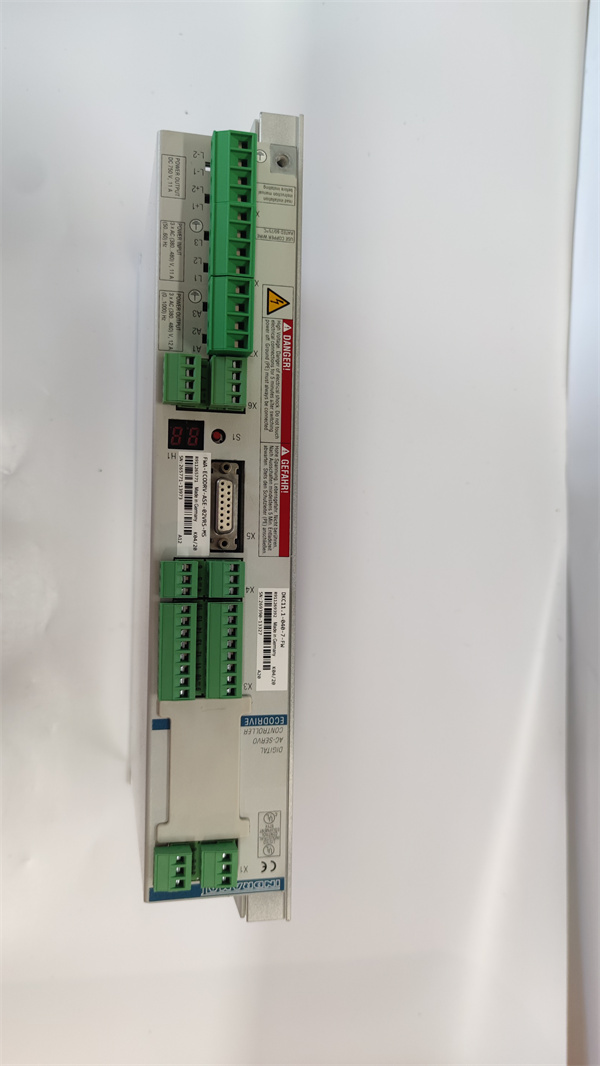
DKC11.1-040-7-FW
When selecting the DKC11.1-040-7-FW, consider:
- Load Requirements: Match the 40 A continuous current and 700 VDC bus voltage to your application’s mechanical demands.
- Environmental Conditions: Use optional cooling solutions for temperatures above 40°C or dust-resistant enclosures for harsh environments.
- Control System Compatibility: Verify analog/parallel interface or fieldbus module compatibility with your PLC or motion controller.
- Budget: Balance upfront costs with long-term savings from energy efficiency and reduced downtime.
- Installation: Follow Rexroth’s guidelines for proper grounding and cable routing to prevent EMI. Use torque wrenches for secure mounting.
- Electrical Safety: Disconnect power before servicing. Use shielded cables for encoder and power connections to ensure signal integrity.
- Maintenance: Clean air vents quarterly to prevent dust accumulation. Check thermal grease and bearings every 20,000 hours.
- Firmware Updates: Regularly update firmware via Rexroth’s software to access new features and bug fixes.
Shanxi Xinyeda International Trade Co., Ltd. is your trusted partner for
REXROTH DKC11.1-040-7-FW and other automation spare parts. We provide comprehensive sales and technical support to optimize your industrial control systems. Visit our website
www.xydcontrol.com or contact us for more information.
Continue Searching
We're here when you need us
What happens next?
- 1. Email confirmation
You will get an email confirming that we have received your enquiry.
- 2. Dedicated Account Manager
One of our team will be in touch to confirm your part(s) specification and condition.
- 3. Your quote
You will receive a comprehensive quote tailored to your specific needs.