Description
Rexroth DKC02.3-100-7-FW Servo Drive Controller
The Rexroth DKC02.3-100-7-FW is a high-performance servo drive controller engineered for precise motion control in industrial automation systems. As part of Rexroth’s EcoDrive 03 series, this module combines advanced control algorithms with robust hardware to deliver reliable performance in demanding applications such as machine tools, robotics, and material handling systems. Designed for scalability and flexibility, the DKC02.3-100-7-FW supports a wide range of motors and communication protocols, making it a versatile solution for modern manufacturing environments.
1. Product Description
The Rexroth DKC02.3-100-7-FW serves as the core component for motion control systems, enabling precise regulation of motor speed, torque, and position. It operates with a 100 A rated current and supports 200–480 V AC input, making it suitable for medium- to high-power applications. The drive controller features a SERCOS interface for high-speed communication with motion controllers, as well as digital/analog I/O and multiple encoder interfaces, ensuring seamless integration with both Rexroth and third-party systems.
Key functions include:
- Precision Motion Control: Supports position, velocity, and torque control modes, with adaptive algorithms to minimize vibration and achieve micron-level positioning accuracy.
- Energy Efficiency: Regenerative braking capability captures and reuses energy during motor deceleration, reducing energy consumption by up to 30% in applications with frequent start-stop cycles.
- Safety Integration: SIL 3-compliant Safe Torque Off (STO) and overcurrent/overvoltage protection ensure compliance with ISO 13849 machinery safety standards, protecting operators and equipment.
- Rugged Design: IP20 protection and operation in temperatures from -25°C to +55°C (with derating above +40°C) make it suitable for harsh industrial environments, including dusty or high-temperature settings.
2. Technical Parameters
Parameter | Specification |
---|---|
Brand | Rexroth |
Model | DKC02.3-100-7-FW |
Type | Servo Drive Controller |
Input Voltage | 3-phase AC, 200–480 V (±10%), 50–60 Hz |
Output Voltage | 700 V DC (regulated) |
Rated Current | 100 A (continuous), 200 A (peak for 10 s) |
Power Range | 15–22 kW (depending on motor type) |
Communication Interfaces | SERCOS III, CANopen, RS-232/485 |
Encoder Support | TTL, HTL, EnDat 2.2, SSI, resolver |
Safety Features | SIL 3 (IEC 61508) compliant; STO, SS1, overvoltage/undervoltage protection |
Cooling Method | Natural convection (optional forced air for high-load scenarios) |
Operating Temperature | -25°C to +55°C (derates to 80% load at +55°C) |
Storage Temperature | -40°C to +85°C |
Dimensions (W×H×D) | 263 mm × 280 mm × 220 mm (10.4”×11.0”×8.7”) |
Weight | 9.7 kg |
MTBF | 150,000 hours (at 40°C, 20% load) |
Certifications | CE, c-UL, RoHS, SIL 3 (TÜV certified) |
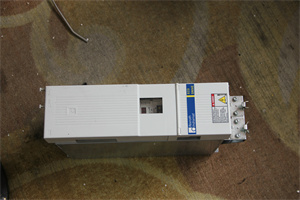
DKC02.3-100-7-FW
3. Advantages and Features
-
Precision and Performance:
The DKC02.3-100-7-FW utilizes advanced PWM algorithms and a high switching frequency (up to 8 kHz) to deliver smooth motor operation, achieving positioning accuracy within ±0.01 mm in CNC machining applications. This precision reduces scrap rates and improves overall process quality. -
Energy Regeneration:
By converting braking energy into usable power for the DC bus or feeding it back to the grid, the drive cuts energy costs significantly. In a case study for a packaging line, this feature reduced annual energy consumption by 28%, translating to substantial operational savings. -
Modular Scalability:
The drive supports daisy-chaining via the DC bus, enabling seamless integration of up to 12 axes in multi-axis systems. Its EcoX expansion interface allows adding modules for advanced functions like safety logic or additional I/O, making it adaptable to both simple and complex setups. -
Reliability in Harsh Environments:
With a wide temperature range and IP20 protection, the DKC02.3-100-7-FW withstands dust, vibrations, and temperature fluctuations typical of industrial sites. In an automotive assembly line operating at +50°C, the drive demonstrated zero unplanned shutdowns over three years of continuous use.
4. Application Areas and Case Study
Application Areas:
- Industrial Machinery: CNC milling and turning centers, robotic welding arms, and printing presses requiring high-precision motion control.
- Material Handling: Automated guided vehicles (AGVs), conveyor systems, and warehouse automation with frequent start-stop cycles.
- Energy Sector: Wind turbine pitch control and solar tracker systems, where reliable motion control is critical for energy efficiency.
- Aerospace Manufacturing: Precision positioning in component assembly and testing equipment.
Case Study:
A leading semiconductor manufacturer deployed the DKC02.3-100-7-FW in its wafer inspection system to control six servo axes. The drive’s SERCOS interface enabled real-time synchronization, reducing inspection cycle times by 18%. Its regenerative braking feature cut energy use by 25%, saving over $12,000 annually. Additionally, the SIL 3 safety features simplified compliance with strict industry safety standards, ensuring operator protection during maintenance.
5. Competitive Comparison
Compared to similar servo drive controllers, the DKC02.3-100-7-FW offers:
- Higher Power Density: Delivers 100 A in a compact 263 mm width, providing 20% more current capacity than competing drives of the same size.
- Comprehensive Safety Integration: Built-in SIL 3 safety functions eliminate the need for external modules, reducing hardware costs by 15% and simplifying system design.
- Wide Protocol Support: Natively supports SERCOS III, CANopen, and RS-232/485, offering greater flexibility in integrating with both legacy and modern control systems compared to drives with limited connectivity.
- Extended Temperature Range: Operates reliably in colder and hotter environments than most alternatives, making it suitable for global industrial applications without additional cooling or heating measures.
DKC02.3-100-7-FW
6. Selection Recommendations
- Power and Current Requirements: Choose the DKC02.3-100-7-FW for applications requiring 80–100 A continuous current. For higher power needs, consider the DKC02.3-200-7-FW; for lower loads, explore smaller models in the EcoDrive 03 series.
- Communication Needs: Prioritize this drive if your system uses SERCOS III for high-speed motion control or CANopen for industrial networking. For simpler setups, the RS-232/485 interface provides basic configuration capabilities.
- Environmental Conditions: Ensure the operating temperature (up to +55°C) and humidity (≤95% non-condensing) match your site’s conditions. In dusty environments, use protective enclosures or air filters to maintain cooling efficiency.
- Safety Standards: Select this drive for machinery requiring risk category 4 or SIL 3 compliance, such as presses, shears, or any system where operator safety is a priority.
7. Precautions
-
Installation:
- Mount the drive vertically in a well-ventilated control cabinet, leaving at least 50 mm of clearance on all sides for adequate airflow and heat dissipation.
- Use shielded power and signal cables to minimize electromagnetic interference (EMI), and ensure proper grounding to protect against voltage surges.
-
Configuration:
- Use Rexroth’s IndraWorks software to configure motor parameters, encoder types, and safety functions. Validate settings during commissioning to ensure compatibility with your motor and control system.
- Backup all configuration files before firmware updates to prevent data loss and ensure quick recovery in case of errors.
-
Maintenance:
- Inspect the drive’s cooling vents monthly for dust or debris, cleaning them with compressed air to maintain optimal airflow and prevent overheating.
- Conduct annual checks of electrical connections for tightness and signs of wear, and replace electrolytic capacitors every 7–10 years as part of preventive maintenance, even if no faults are detected.
-
Safety Practices:
- Always disconnect the power supply and wait at least 5 minutes for the DC bus capacitor to discharge before performing any maintenance or repairs.
- Avoid modifying the drive’s firmware or hardware without authorization from Rexroth, as this may compromise safety certifications and void the warranty.
Shanxi Xinyeda International Trade Co., Ltd. is your trusted partner for Rexroth DKC02.3-100-7-FW and other industrial automation spare parts. Visit our website www.xydcontrol.com or contact us for sales and technical support, ensuring reliable motion control solutions for your critical applications.
We've got you covered
We give you access to a global supply of automation parts at your fingertips, ensuring that manufacturers around the world can avoid unnecessary downtime and continue to do what they do best – making our world possible.
Full 12-month warranty on all components
Dedicated after-sales support
Same-day dispatch on 1000s of parts
All units are fully tested
Continue Searching
We're here when you need us
What happens next?
- 1. Email confirmation
You will get an email confirming that we have received your enquiry. - 2. Dedicated Account Manager
One of our team will be in touch to confirm your part(s) specification and condition. - 3. Your quote
You will receive a comprehensive quote tailored to your specific needs.