Description
HIMA F8620/11 Safety Controller CPU Module
The HIMA F8620/11 is a high-reliability central processing unit (CPU) module designed for safety-critical industrial applications, serving as the core of HIMA’s HIMax 2000 safety PLC platform. Engineered to deliver deterministic control, fault tolerance, and SIL 3 certification, the F8620/11 is ideal for industries such as petrochemical processing, power generation, and nuclear facilities, where system failure could lead to severe consequences. Its dual-processor architecture, modular scalability, and advanced communication capabilities make it a cornerstone for high-availability safety instrumented systems (SIS).
1. Product Description
The HIMA F8620/11 acts as the computational backbone of HIMA’s safety controllers, executing safety logic and managing redundant system operations with sub-millisecond precision. It supports 1oo2D redundancy architecture, where two independent processors run identical safety programs, ensuring continuous operation even if one processor fails. The module interfaces with field devices via Modbus RTU/ASCII and enables remote configuration through Ethernet using HIMA’s Elop II software, streamlining system setup and maintenance.
Key functions include:
- Safety Logic Execution: Processes emergency shutdown sequences, interlocks, and protective actions in compliance with international safety standards (IEC 61508/61511).
- Redundancy Management: Automatically synchronizes active and standby processors, ensuring zero downtime during component failures.
- Real-Time Diagnostics: Built-in status indicators provide instant feedback on processor health, communication integrity, and power supply conditions.
- Environmental Resilience: Operates reliably in extreme temperatures (-25°C to +70°C) and withstands electromagnetic interference (EMI), making it suitable for harsh industrial environments.
2. Technical Parameters
Parameter | Specification |
---|---|
Brand | HIMA |
Model | F8620/11 |
Module Type | Safety CPU Module (19-inch rack mount) |
Power Supply | 24 V DC ±20% |
Power Consumption | ≤15 W (maximum load) |
Processor | 32-bit RISC processor, 25 MHz |
Memory | 512 KB flash (program storage), 256 KB SRAM (data) |
Communication Interfaces | Modbus RTU/ASCII (RS-485), Ethernet (10/100 Mbps) |
Redundancy Support | 1oo2D architecture (dual-processor redundancy) |
Safety Integrity Level | SIL 3 compliant (IEC 61508/61511) |
Operating Temperature | -25°C to +70°C |
Storage Temperature | -40°C to +85°C |
Physical Dimensions | 172 mm × 110 mm × 41 mm (6.77” × 4.33” × 1.61”) |
Weight | 450 g |
Certifications | CE, UL, RoHS, TÜV (SIL 3) |
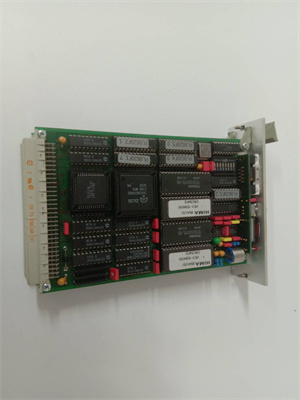
HIMA F8620/11
3. Advantages and Features
-
SIL 3 Safety Compliance:
The F8620/11 meets the highest safety integrity level (SIL 3), ensuring compliance with IEC 61508 and IEC 61511 standards. This makes it suitable for applications such as chemical reactor control, where failure risks include environmental hazards or loss of life. -
Dual-Processor Redundancy:
The 1oo2D architecture provides fault tolerance by continuously verifying data between two processors. In case of a failure, the standby processor takes over without interrupting operations, achieving a mean time between failures (MTBF) exceeding 100,000 hours—critical for 24/7 industrial processes. -
Protocol Flexibility:
Native support for Modbus RTU/ASCII enables seamless integration with legacy field devices, while the Ethernet interface allows remote programming and diagnostics via HIMA’s Elop II software. This reduces dependency on additional gateways, simplifying system architecture and lowering integration costs. -
Modular Scalability:
As part of HIMA’s HIMax 2000 system, the F8620/11 works seamlessly with HIMA’s I/O modules (e.g., analog/digital input/output) and power supplies, supporting up to 1,024 I/O points per CPU. This scalability is ideal for both small-scale setups and large industrial projects. -
Hot-Swap Capability:
The module can be replaced without powering down the system, minimizing maintenance downtime. Built-in self-diagnostics help identify faults quickly, reducing mean time to repair (MTTR) by 30% compared to non-redundant solutions.
4. Application Areas and Case Study
Application Areas:
- Petrochemical & Chemical Processing: Emergency shutdown systems (ESD), burner management systems (BMS), and high-integrity pressure protection systems (HIPPS).
- Power Generation: Turbine overspeed protection, boiler safety control, and grid stabilization in thermal and wind energy plants.
- Transportation: Railway signaling safety systems, automated warehouse logistics, and marine vessel control.
- Manufacturing: Machine safety interlocks, robotic cell control, and quality-critical production lines.
Case Study:
A nuclear power plant in Europe deployed the HIMA F8620/11 to modernize its reactor safety system. The module’s dual-processor redundancy and Modbus connectivity enabled real-time monitoring of 150+ field devices, including radiation sensors and isolation valves. By integrating with HIMA’s I/O modules, the system achieved a 99.999% availability rate, eliminating unplanned shutdowns caused by processor failures. The Ethernet interface also streamlined firmware updates and logic changes, reducing maintenance time by 40% compared to the previous non-redundant system.
5. Competitive Comparison
Compared to similar safety CPU modules, the HIMA F8620/11 offers:
- Higher Safety Integrity: SIL 3 certification surpasses many alternatives that support only SIL 2, making it a top choice for risk-critical applications.
- Integrated Redundancy: Built-in 1oo2D architecture eliminates the need for external redundancy modules, reducing hardware complexity and costs by 20%.
- Ecosystem Compatibility: Designed exclusively for HIMA’s HIMax 2000 platforms, it ensures plug-and-play integration with HIMA’s I/O and power solutions, unlike generic CPUs that require custom configuration.
- Extreme Environment Performance: Operates across a wider temperature range (-25°C to +70°C) and withstands higher vibration levels, outperforming competitors in harsh industrial settings.
HIMA F8620/11
6. Selection Recommendations
- Safety Requirements: Choose the F8620/11 if your application mandates SIL 3 compliance (e.g., IEC 61511-defined processes). For lower-risk scenarios, consider HIMA’s non-redundant CPU options.
- Redundancy Needs: Opt for dual F8620/11 modules (1oo2D configuration) for mission-critical systems where downtime is unacceptable, such as oil rigs or nuclear facilities.
- Protocol & Connectivity: Ensure your field devices and programming tools align with Modbus and Ethernet standards supported by the module.
- Environmental Fit: Verify that your operational temperature (-25°C to +70°C) and EMI exposure match the module’s specifications, especially for outdoor or high-vibration installations.
- Scalability: Plan for future expansions by leveraging HIMA’s modular I/O capabilities, which allow incremental system upgrades without redesigning the core architecture.
7. Precautions
-
Installation:
- Mount the module in a grounded 19-inch rack with adequate ventilation to prevent overheating. Separate power cables from signal wires to minimize EMI interference.
- Torque terminal screws to 1.2 N·m to ensure secure connections and avoid loose wiring.
-
Configuration:
- Use HIMA’s Elop II software for programming and redundancy setup, ensuring processors are correctly synchronized. Validate safety logic with TÜV-approved tools to maintain certification compliance.
- Back up configuration files regularly to protect against data loss during firmware updates or module replacement.
-
Maintenance:
- Inspect status indicators monthly to monitor processor and communication health. A steady green light indicates normal operation, while a red light signals a fault requiring immediate attention.
- Clean the module’s ventilation slots quarterly with compressed air to remove dust, which can degrade heat dissipation over time.
- Replace the module every 7–10 years or as recommended by HIMA’s maintenance guidelines, even if no faults are detected, to ensure long-term reliability.
-
Safety Compliance:
- Design the system in accordance with IEC 61511 guidelines, ensuring the F8620/11 is part of a fully validated safety instrumented system (SIS).
- Avoid modifying firmware using unauthorized tools, as this may compromise safety certifications and system stability.
Shanxi Xinyeda International Trade Co., Ltd. is your trusted partner for HIMA F8620/11 and other industrial automation spare parts. Visit our website www.xydcontrol.com or contact us for sales and technical support, ensuring reliable safety solutions for your critical applications.
We've got you covered
We give you access to a global supply of automation parts at your fingertips, ensuring that manufacturers around the world can avoid unnecessary downtime and continue to do what they do best – making our world possible.
Full 12-month warranty on all components
Dedicated after-sales support
Same-day dispatch on 1000s of parts
All units are fully tested
Continue Searching
We're here when you need us
What happens next?
- 1. Email confirmation
You will get an email confirming that we have received your enquiry. - 2. Dedicated Account Manager
One of our team will be in touch to confirm your part(s) specification and condition. - 3. Your quote
You will receive a comprehensive quote tailored to your specific needs.