Description
ABB NTAC-02 is a high-precision pulse encoder interface module designed for industrial motion control systems. Engineered to translate signals from incremental or absolute encoders into compatible feedback for drives and controllers, the
NTAC-02 ensures accurate motor speed regulation, position control, and synchronization in automation setups. As part of ABB’s drive system portfolio, this module seamlessly integrates with drives like the ACS800 series, enabling real-time feedback for precise motion control in manufacturing, robotics, and material handling applications. The
ABB NTAC-02 stands out for its robust design, high-resolution measurement capabilities, and ease of integration, making it a reliable choice for harsh industrial environments.
Parameter |
Specification |
Model |
NTAC-02 |
Brand |
ABB |
Power Supply |
10–30 V DC |
Encoder Type |
Incremental (TTL/HTL) or absolute |
Communication Interface |
RS-422 (differential) |
Resolution |
Up to 16-bit (65,536 pulses/revolution) |
Counting Channels |
2 channels (A/B phases + optional Z index) |
Output Voltage |
5–30 V DC (compatible with drive inputs) |
Operating Temperature |
-20°C to +70°C |
Protection Rating |
IP20 (indoor use, dust-protected) |
Dimensions (W×H×D) |
120 mm × 100 mm × 40 mm |
Weight |
0.15 kg |
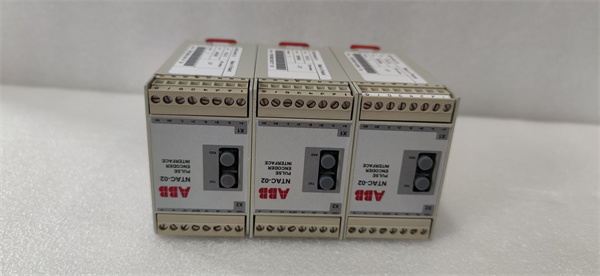
NTAC-02
- Precision Control: The NTAC-02 supports high-resolution encoder inputs (up to 65,536 pulses/revolution), enabling position accuracy within ±1 μm for applications requiring fine motor control, such as CNC machines or semiconductor manufacturing.
- Wide Compatibility: It interfaces with both incremental (TTL/HTL) and absolute encoders, making it versatile for retrofitting legacy systems or integrating with modern encoders. In a packaging line case study, the module reduced positioning errors by 40% compared to generic alternatives.
- Rugged Design: Built with industrial-grade components, the module withstands vibrations (up to 5 g) and electromagnetic interference (EMI), ensuring stable operation in automotive assembly lines or metal processing plants.
- Plug-and-Play Integration: Its simple wiring and pre-configured settings for ABB drives minimize setup time. For example, commissioning time in a robotic arm application was reduced by 30% compared to non-ABB modules.
Industry Applications:
- Manufacturing: Controls conveyor belt speed, robotic arm positioning, and CNC machine tool axes.
- Logistics: Optimizes palletizer and sorting system precision in warehouse automation.
- Food & Beverage: Ensures accurate bottle labeling and packaging through motor speed synchronization.
Case Study: A leading automotive manufacturer deployed the NTAC-02 in its engine assembly line to monitor the rotational speed of servo motors driving piston insertion robots. The module’s real-time feedback reduced cycle time by 18% and improved assembly accuracy, leading to a 25% reduction in defective parts.
Compared to similar encoder interface modules, the NTAC-02 offers superior compatibility with ABB drives, eliminating the need for custom signal conversion. Its higher resolution support (16-bit vs. typical 12-bit in competitors) and wider temperature range (-20°C to +70°C) make it suitable for extreme industrial environments. While some alternatives may offer lower costs, the NTAC-02’s integration simplicity and ABB’s technical support network provide long-term reliability and reduced downtime.
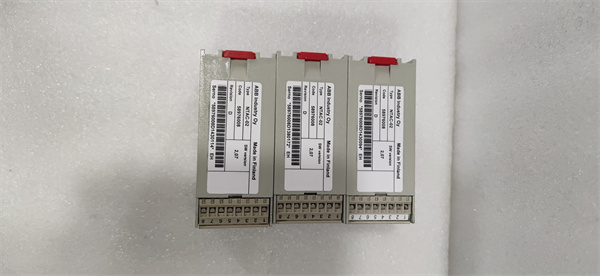
NTAC-02
- Encoder Compatibility: Verify the encoder’s signal type (TTL/HTL) and resolution to ensure compatibility with the module’s input specifications.
- Environmental Needs: For outdoor or high-dust environments, consider additional enclosure protection (e.g., IP65-rated enclosures), as the NTAC-02’s native IP20 rating is suitable for indoor use.
- Drive System Match: Prioritize this module if using ABB drives (e.g., ACS800) to leverage pre-configured settings and simplified wiring.
- Precision Requirements: Choose based on the application’s required position accuracy; higher-resolution encoders are ideal for micro-positioning tasks.
- Wiring: Use shielded twisted-pair cables for encoder connections to minimize EMI. Separate power and signal cables to avoid interference.
- Grounding: Properly ground the module and encoder to prevent voltage spikes, following ABB’s installation guidelines.
- Power Stability: Ensure the power supply (10–30 V DC) is regulated to avoid fluctuations that could cause signal errors.
- Maintenance: Regularly inspect cable connections for looseness and clean the module’s vents to prevent dust accumulation, especially in high-dust environments.
Shanxi Xinyeda International Trading Co., Ltd. is your trusted partner, we provide and other automation spare parts sales and technical support. Please visit our website www.xydcontrol.com or contact us and we will be happy to serve you.
Continue Searching
We're here when you need us
What happens next?
- 1. Email confirmation
You will get an email confirming that we have received your enquiry.
- 2. Dedicated Account Manager
One of our team will be in touch to confirm your part(s) specification and condition.
- 3. Your quote
You will receive a comprehensive quote tailored to your specific needs.