Description
The
ABB LTC391AE01 HIEE401782R0001 is a high-precision
linear motor control module designed for advanced industrial automation systems, particularly those requiring ultra-precise motion control in semiconductor manufacturing, electronics assembly, and medical device production. As part of ABB’s
Motion Control portfolio, this module belongs to the
LTC300 series, engineered to deliver deterministic performance and seamless integration with ABB’s drives and robotics platforms. The
LTC391AE01 HIEE401782R0001 serves as the core controller for linear motors, enabling sub-micron positioning accuracy and high-speed motion profiles while maintaining exceptional stability.
Featuring a compact, fanless design and advanced digital signal processing (DSP), the ABB LTC391AE01 HIEE401782R0001 supports multiple control modes, including position, velocity, and torque control, with compatibility for linear encoders (e.g., optical or magnetic scales) to achieve closed-loop feedback. Its core functions include real-time trajectory planning, vibration suppression, and dynamic gain scheduling, ensuring smooth motion even at high accelerations (up to 10 g). Positioned as a premium solution for high-precision industries, the module reduces cycle times by up to 20% while enhancing product quality through minimized positioning errors. By integrating with ABB’s RobotStudio® software, it enables offline programming and simulation, further optimizing deployment efficiency.
Parameter Name |
Parameter Value |
Product Model |
LTC391AE01 HIEE401782R0001 |
Manufacturer |
ABB |
Product Type |
Linear Motor Control Module |
Control Modes |
Position, velocity, torque |
Feedback Resolution |
Up to 1 nm (with compatible encoders) |
Maximum Output Current |
30 A (peak), 20 A (continuous) |
Voltage Range |
48–80 V DC |
Communication Interface |
EtherCAT, SERCOS III, Modbus TCP |
Processing Power |
Dual-core ARM Cortex-A9 @ 1 GHz |
Operating Temperature |
5°C to +45°C (with derating up to +50°C) |
Dimensions (W×H×D) |
140 mm × 200 mm × 60 mm |
Mounting Method |
Panel mounting (horizontal/vertical) |
Certification |
CE, UL, ISO 14644-1 (cleanroom compliant) |
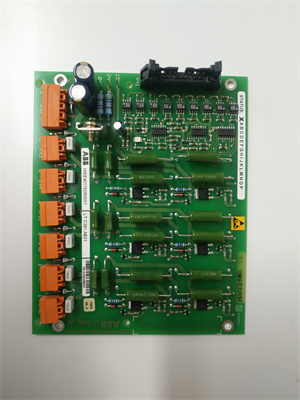
LTC391AE01 HIEE401782R0001
The ABB LTC391AE01 HIEE401782R0001 distinguishes itself through its exceptional precision and dynamic performance. Its advanced DSP algorithms enable real-time compensation for mechanical imperfections, such as cogging and backlash, resulting in positioning accuracy within ±0.1 μm. The module’s support for high-bandwidth EtherCAT communication (up to 100 Mbps) ensures minimal latency, critical for multi-axis synchronization in complex pick-and-place systems.
A key advantage is the module’s compatibility with ABB’s ACQ500 servo drives, forming a fully integrated motion control solution. This integration reduces wiring complexity and ensures optimal performance matching between the controller and drive. The LTC391AE01 HIEE401782R0001 also features built-in safety functions, including safe torque off (STO) and safe stop 1 (SS1), compliant with ISO 13849-1 (PLd), making it suitable for collaborative robotics and human-robot interaction scenarios.
The module’s compact form factor and fanless design make it ideal for space-constrained cleanroom environments (e.g., ISO Class 5), where dust and particle generation must be minimized. Its rugged construction, with conformal coating and reinforced connectors, ensures reliability in high-vibration or high-humidity settings, such as automotive assembly lines or pharmaceutical packaging facilities.
The ABB LTC391AE01 HIEE401782R0001 is indispensable in industries demanding sub-micron precision and repeatability. In semiconductor manufacturing, it controls wafer handling robots, inspection stages, and die bonders, ensuring accurate placement of components during chip fabrication. For electronics assembly, the module drives pick-and-place machines to position surface-mount devices (SMDs) with precision, reducing defects in PCBA production.
In the medical device industry, the LTC391AE01 HIEE401782R0001 enables the assembly of microfluidic devices, surgical instruments, and diagnostic equipment, where dimensional accuracy is critical for product functionality. It also excels in research and development applications, such as nanotechnology labs and metrology systems, where precise motion control is essential for experimental setups.
By addressing the challenges of high-speed, high-precision motion in sensitive environments, the module helps customers achieve tighter process tolerances, improve yield rates, and accelerate time-to-market for advanced products. Its scalability and adaptability make it a future-proof solution for evolving automation needs, from legacy systems to cutting-edge smart factories.
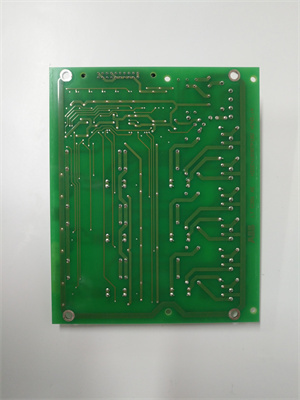
LTC391AE01 HIEE401782R0001
- ABB LTC380AE01 HIEE401781R0001: A cost-effective variant for basic linear motor control, supporting lower current ranges (up to 15 A).
- ABB ACQ500-01E 3BSE042600R1: A servo drive specifically designed for use with the LTC391AE01, offering high-power density and EtherCAT connectivity.
- ABB IRB 910INV: A collaborative industrial robot that integrates with the LTC391AE01 for precision assembly tasks in confined spaces.
- ABB AM601 Encoder: A high-resolution optical encoder (1 nm resolution) compatible with the LTC391AE01 for closed-loop feedback.
- ABB RobotStudio® Motion Control Add-On: Software extension for programming and simulating linear motor trajectories with the LTC391AE01.
- ABB SafeMove2 Software: A safety software package that enhances the LTC391AE01’s safety features for collaborative applications.
Pre-installation preparation: Mount the ABB LTC391AE01 HIEE401782R0001 in a grounded control panel within a cleanroom or controlled environment, ensuring proper heat dissipation (minimum 20 mm clearance on all sides). Connect the module to the linear motor’s power cables and encoder feedback using shielded, low-capacitance wiring to minimize noise. Configure the control mode, encoder type, and communication protocol (e.g., EtherCAT) via ABB’s Drive composer software, calibrating the system using a reference position sensor.
Maintenance recommendations: Regularly inspect the module’s status LEDs for fault codes (e.g., overcurrent, overheating) and use Drive composer to monitor motor parameters, such as winding temperature and current harmonics. Clean the module’s surface with a static-free cloth to prevent dust accumulation in cleanroom environments. Update the firmware quarterly to incorporate new motion control algorithms and safety patches. In the event of a fault, replace the module with a pre-calibrated spare, ensuring the new unit is configured with identical parameters to maintain process consistency.
ABB stands behind the LTC391AE01 HIEE401782R0001 with a comprehensive quality assurance program, including rigorous testing for precision, EMC compliance, and safety functionality. The module is backed by a standard [X-year] warranty, covering defects in materials and workmanship. ABB’s global technical support team provides 24/7 assistance for configuration, troubleshooting, and on-site calibration, ensuring minimal downtime in high-precision production lines. Customers can leverage ABB’s Remote Services for real-time health monitoring and predictive maintenance insights via the ABB Ability™ platform. With a commitment to innovation and reliability, ABB ensures the LTC391AE01 HIEE401782R0001 delivers unmatched performance in the most demanding industrial applications.
Shanxi Xinyeda International Trading Co., Ltd. is your trusted partner, we provide and other automation spare parts sales and technical support. Please visit our website www.xydcontrol.com or contact us and we will be happy to serve you.
Continue Searching
We're here when you need us
What happens next?
- 1. Email confirmation
You will get an email confirming that we have received your enquiry.
- 2. Dedicated Account Manager
One of our team will be in touch to confirm your part(s) specification and condition.
- 3. Your quote
You will receive a comprehensive quote tailored to your specific needs.