Description
The
ABB 500MTM02 1MRB150020R0712 1HDF930512X010 is a high-performance
motor thermal management and protection system designed for ABB’s advanced industrial motor control ecosystems. As a cornerstone of the
Motor Condition Monitoring (MCM) portfolio, this system integrates thermal modeling, real-time diagnostics, and predictive analytics to safeguard motors against overloads, insulation degradation, and thermal stress. The
500MTM02 leverages the
1MRB150020R0712 firmware variant and
1HDF930512X010 hardware configuration to deliver precision monitoring across 12 thermal channels, supporting PTC/NTC sensors, RTDs (Pt100/1000), and direct winding temperature calculations. Engineered for industries requiring 24/7 uptime—such as mining, oil & gas, and power generation—the system acts as a critical interface between motors and ABB’s
800xA DCS or
AC 500 PLC, enabling proactive maintenance and reducing unplanned downtime by up to 50%.
The 500MTM02 1MRB150020R0712 1HDF930512X010 features a rugged IP65-rated enclosure and galvanic isolation (500 V rms), ensuring reliability in harsh environments with high vibration, moisture, or EMI. Its modular design supports hot-swappable channel cards, simplifying repairs without system shutdown, while the intuitive web interface (via Ethernet/IP) provides real-time insights into motor health metrics, such as stator temperature trends, bearing wear indicators, and thermal reserve margins. Positioned as a future-proof solution, the system complies with IEC 60204-1 safety standards and integrates seamlessly with ABB’s Ability™ Predictive Maintenance software, transforming raw sensor data into actionable insights for lifecycle management.
Parameter Name |
Parameter Value |
Product Model |
500MTM02 1MRB150020R0712 1HDF930512X010 |
Manufacturer |
ABB |
Product Type |
Motor Thermal Management System |
Thermal Channels |
12 isolated (6 stator + 6 bearing) |
Sensor Types |
PTC/NTC thermistors, RTDs (Pt100/1000), TC (J/K/T) |
Thermal Modeling |
I²t-based winding temperature prediction |
Communication |
Modbus RTU, Profibus DP, Ethernet/IP (IEEE 802.3) |
Power Supply |
24 V DC (±15%) or 100–240 V AC (auto-sensing) |
Operating Temperature |
-40°C to +70°C |
Dimensions (W×H×D) |
220 mm × 180 mm × 100 mm |
Mounting Method |
Panel-mounted or DIN rail (with brackets) |
Certification |
CE, UL, IEC 61508 (SIL 2), ATEX (Zone 2) |
Alarm/Trip Outputs |
4 relay outputs (SPDT, 5 A/250 V AC) |
The 500MTM02 uses adaptive I²t algorithms to simulate motor winding temperatures in real time, even without direct sensor installation. This feature is critical for submerged pumps in wastewater treatment plants or hard-to-reach motors in mining conveyors. The system’s dynamic load compensation adjusts trip thresholds based on motor loading profiles, preventing false trips during normal startup inrush while ensuring rapid response to genuine overloads—e.g., in a paper mill’s calender rolls, where sudden sheet jams could cause overheating.
Integrated with ABB’s Machine Learning Predictive Models, the 1MRB150020R0712 firmware analyzes historical temperature data to identify early signs of bearing failure (e.g., rising kurtosis in vibration spectra) or stator winding degradation (e.g., increasing thermal resistance). In a petrochemical plant, this capability detected a failing motor in a glycol dehydration unit 72 hours before a critical failure, allowing maintenance during a scheduled shutdown. The 1HDF930512X010 hardware includes a built-in web server for remote access via smartphones or SCADA systems, enabling technicians to monitor motor health from anywhere in the plant.
The IP65 enclosure and conformal-coated PCBs of the
500MTM02 protect against dust, water jets, and corrosive gases, making it suitable for offshore platforms or cement production lines. The system’s dual-power input (DC/AC) and redundant communication ports (Ethernet/IP + Profibus DP) enhance reliability in critical applications like nuclear power plant cooling systems. Hot-swappable channel cards reduce MTTR to under 15 minutes, while the front-panel OLED display provides at-a-glance status updates without needing external software.
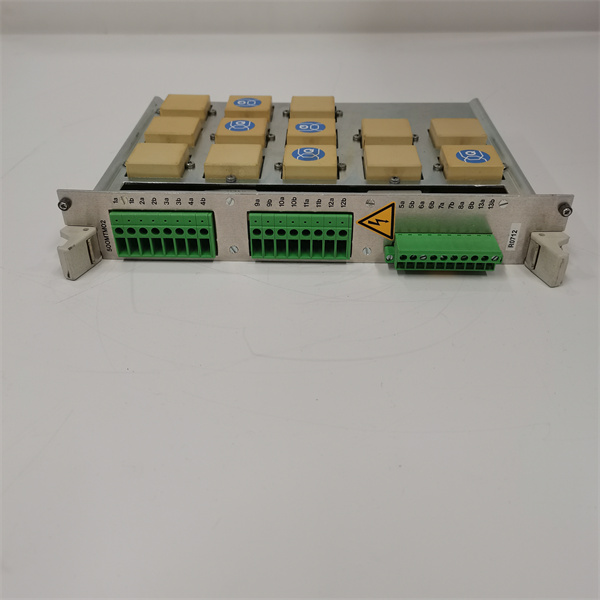
500MTM02 1MRB150020R0712 1HDF 930512 X010
The ABB 500MTM02 1MRB150020R0712 1HDF930512X010 excels in mission-critical applications across industries:
- Oil and Gas: Monitors subsea pumps, compressors, and ESP (electrical submersible pumps) in offshore rigs, with ATEX certification ensuring safety in explosive atmospheres. The system’s wide temperature range supports Arctic installations where motors must operate at -30°C.
- Power Generation: Protects steam turbine-driven feedwater pumps and generator exciters in thermal power plants. Its SIL 2 compliance meets safety requirements for emergency shutdown systems (ESD).
- Mining and Metals: Used in high-power draglines, ball mills, and smelter motors, where thermal runaway risks are high. The system’s vibration-resistant design (IEC 60068-2-6) withstands continuous mechanical stress in mineral processing.
- Pharmaceuticals: Ensures precise temperature control in sterilization autoclaves and freeze dryers, with 21 CFR Part 11-compliant data logging for regulatory compliance. The system’s low electromagnetic emissions (EN 55011) prevent interference with sensitive lab equipment.
- ABB 500MTM01 1MRB150019R0601 1HDF930511X001: A 6-channel variant for smaller motors, ideal for HVAC systems or packaging lines.
- ABB 1MRB150021R0813 1HDF930513X020: Upgraded firmware with AI-driven anomaly detection, compatible with ABB’s Ability™ Condition Monitoring Solution.
- ABB PM866AK01: AC 800M control module for integrating thermal data with process control logic.
- ABB TB532: Explosion-proof terminal block for sensor wiring in hazardous areas, compatible with the 500MTM02.
- ABB CM606: Wireless vibration monitoring module, complementary for holistic motor health analysis.
Pre-installation preparation: Mount the 500MTM02 on a grounded panel using the provided brackets, ensuring at least 50 mm clearance for airflow. Terminate sensor cables with shielded twisted-pair wiring, following the color-coded diagram in the 1HDF930512X010 manual. Configure sensor types and alarm thresholds via the web interface or ABB’s Control Builder M software, and validate communication with the PLC/DCS using built-in ping tools. For hazardous areas, ensure all connections comply with ATEX wiring guidelines.
Maintenance recommendations: Perform visual inspections quarterly, checking for loose terminals or enclosure seal degradation. Use the system’s Self-Test Function monthly to verify relay outputs and ADC accuracy. In dusty environments (e.g., grain silos), clean the enclosure vents with compressed air every six months. Update firmware annually via the web interface to access new sensor algorithms or cybersecurity patches. For RTD channels, recalibrate against a reference thermometer every two years to maintain ±0.5°C accuracy.
ABB guarantees the 500MTM02 1MRB150020R0712 1HDF930512X010 with a 5-year warranty, covering defects in materials, firmware, and workmanship. ABB’s Global Service Network provides 24/7 remote diagnostics and emergency onsite support, with average response times under 4 hours for critical failures. The system undergoes rigorous testing, including 1,000-hour thermal cycling and 100,000-cycle relay life tests, ensuring compliance with ISO 9001 standards. For customers in regulated industries, ABB offers Validation Packages that include factory acceptance testing (FAT) and site-specific risk assessments, ensuring the system meets project-specific safety and performance criteria. By combining cutting-edge thermal management with industrial-grade durability, the 500MTM02 delivers unmatched value for organizations prioritizing operational resilience and energy efficiency.
Shanxi Xinyeda International Trading Co., Ltd. is your trusted partner, we provide and other automation spare parts sales and technical support. Please visit our website www.xydcontrol.com or contact us and we will be happy to serve you.
Continue Searching
We're here when you need us
What happens next?
- 1. Email confirmation
You will get an email confirming that we have received your enquiry.
- 2. Dedicated Account Manager
One of our team will be in touch to confirm your part(s) specification and condition.
- 3. Your quote
You will receive a comprehensive quote tailored to your specific needs.